'lost wax' the ancient art of cire perdu
Talos Art Foundry casts bronze sculpture using the lost wax technique (cire perdue). Lost wax casting was first used by the Ancient Egyptians around 2500BC and the technique remains largely unchanged.
​
This detail from the tomb of Rekhmira at Luxor dated 1500BC shows foundry workers stoking a charcoal furnace using bellows tied to their feet and lifting a crucible of molten bronze from the fire using long poles much as we still do today.
The
Casting
Process
A complex and involved process, casting has many stages.
See below the steps and technique we use here at the Talos Bronze Art Casting Foundry today.
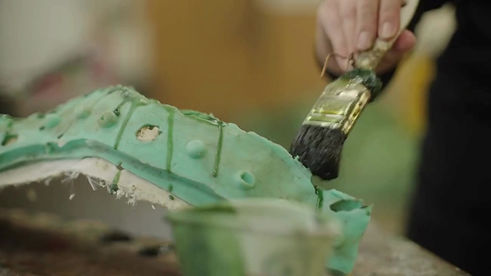

Mould-making
Mould making: the first step of the bronze casting process is to make a mould of the artist’s original sculpture (often in clay or a 3D plastic).
We use modern Silicone rubber moulding materials so sensitive that the artist’s fingerprints can sometimes appear in the finished bronze sculpture. Around the sillicone we use plaster or Jesmonite as a 'jacket' to hold the rubber in place.
​
At this stage large sculptures are made as single moulds. Once they have been cast in wax the team will assess the best way to carve them up into multiple sections so that they can be cast in bronze and then 'chased' back together.
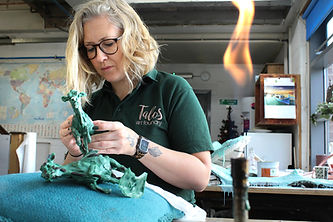
Wax modelling & dipping
We make a hollow wax (approx. 5mm thick) from the mould which is a reproduction of the original sculpture and using hot tools we ‘touch up’ the seam line and any imperfections on the surface of the wax. The artist is invited in to inspect the wax and they can do some minor alterations at this stage.
​​
RUN UP
‘Run up’ is essentially the first stage of making a mould for the molten bronze. Often the wax is kept in one piece if it is within our size limit, but if it is larger it will be cut into several pieces (the size limit is there because our crucibles can only hold 40kg of molten metal per pour).
The wax is attached to the pouring cup with a series of wax tubes called 'sprues' or runners that will eventually feed the metal into the shell and a riser is added to let any trapped air out of the shell. To ensure a piece is cast hollow, we have to put metal pins into the wax and cut a small window or patch into it that we cover with wax paper.
​​
INVESTMENT or DIPPING
The 'run up' waxes are then dipped or ‘invested’ - covered in a liquid ceramic material that dries on the surface of the wax to pick up the detail, much like the rubber does in the mould. They are dipped several more times and sprinkled with a granular ceramic material for strength and allowed to dry thoroughly between each dip.
CASTING HOLLOW
When finished/completely dry and, if they are to be cast hollow, the paper window is tapped out and a different ceramic material called a core mix is poured inside the hole which sets inside the wax and is suspended by the pins. Some pieces such as bases or larger pieces that are cut up will be cast without a core mix as they will be an open form that will allow air to circulate inside and around them. The other exception to casting hollow bronzes is small objects like the door knockers that are cast solid. Although dry at this stage the shells are called ‘green’ until they are fired..





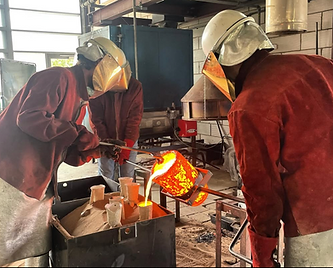
Bronze Casting
KILN
To cast the shells they are placed in groups in the ‘de-waxer’ a large, adapted ceramic kiln. The heat from the de-waxer fires the shells and melts out the wax until you are left with a hollow shell for the metal which is why it is called the lost wax process. The evacuated wax is filtered and recycled.
​​
SAND BOX
We only cast silicon bronze and this is melted in the furnace in a carbon crucible. When the shells are hot and ‘burnt-out’ (no wax remaining and clean inside) they are placed into the casting box in their groups and supported with sand (this helps to keep the heat in the shell and prevent any shells that might burst from injuring the casting team).
POURING
The metal is poured into the cup of the shell and it travels down the runners to fill the shell whilst pushing the air out through the riser. Three people are needed to cast as we use a two-man shank (the shank holds the crucible for pouring the metal). The person holding the two handled end is pouring the metal and the ‘single end’ is held with both hands by the other person who is supporting the weight of the full crucible. The third person is the skimmer who skims any impurities from the metal before pouring and ensures that no lumps or impurities enter the cup whilst the metal is being poured.
​​

Fettling, Chasing & Welding
Chasing is the term used for working the metal with a variety of hand and power tools to disguise the welding and replicate the artists marks and/or texture. It is our aim to reproduce the artists original in bronze as faithfully as possible.
​​​
Once the metal has solidified and cooled it is taken into the fettling shop and allowed to cool completely. Fettling involves knocking the shell off, cutting off the cup, runners and risers (these are cleaned and recycled), removing the metal pins and core mix inside the bronze and then sand blasting the surface.
​
Chasing or 'Ciselure' is a technique where hammering the reverse side of the malleable metal creates a raised or sunken design without removing any material. Sculptures by their very nature are 3D and the chaser plays a key role in ensuring the relief is as the artist intended.
​
Large sculptures are cast in several sections and then joined together and finished by welding. This is where the engineering brain comes in to play as calculating weights and angles to create the correct join will ensure that the work stays 'standing up' for many many years to come.
Patina finishes
Our patination room is always a talking point…the colours on the wall chart to the array of colours on the walls after many years of application is a work of art in itself.
Applying a patina is done with heat and chemicals that are brushed/stippled onto the surface of the bronze and are then sealed with wax or lacquer, or both depending on their location. Once coloured and cooled down, the artist can take the bronze away on the same day.
WHAT IS BRONZE PATINA?
​
Patina is a thin layer that forms on the surface of bronze (and other metals) over time. It’s a natural result of bronze’s exposure to air, water, and other environmental factors.
There is evidence to suggest that once finished, ancient bronzes were brightly painted – the antique patinas that we see today are simply the effect of time and the elements on the bronze during the centuries since the paint faded away.
This effect contributes to the unique character and aesthetic of bronze sculptures and reproducing the antique look is a process we specialise in here at Talos.
We encourage artists to take part in the patination process – overseeing the burnishing of their work and even bringing in their clients for colour selection – much like the relationship between artist and foundry in Ancient Greece where the practice first started.
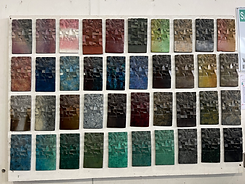
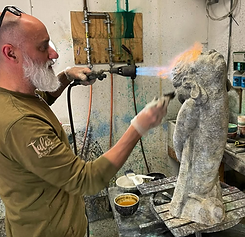
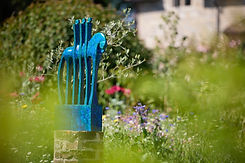
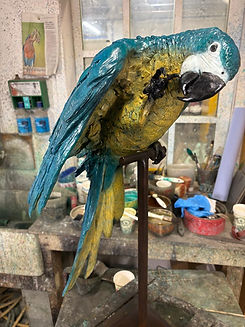
FEATURED ARTIST
Rebecca
Hawkins
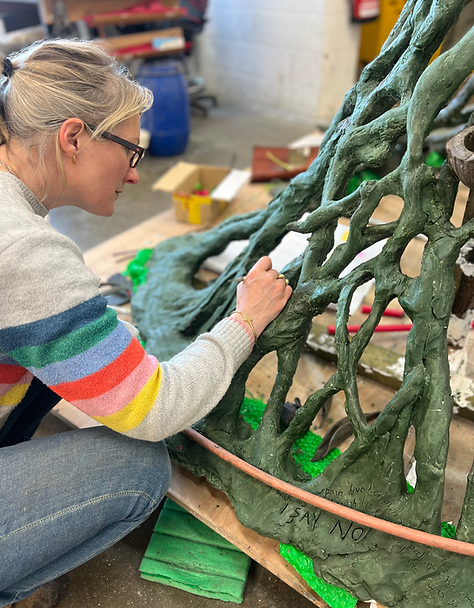
Artist Rebecca Hawkins tells powerful human stories celebrating freedom, and courage, through bronze and charcoal.
​
Her current work 'Petrified survivors' memorial is being modelled and cast here at Talos and will be unveiled outside the The Hague.
Her work has been inspired by 1000s of women's survivor stories of strength through adversity and champion our innate need for freedom.
